What is aluminum extrusion?
Oval aluminum extrusion is the process of pressing aluminum alloy material through a mold with a specific cross-sectional profile. A powerful punch pushes aluminum through the die and then comes out of the die opening. When finished, it will come out in the same shape as the mold and pull out along the beating table. The force applied can be compared to the force applied when a tube of toothpaste is squeezed with your fingers.
What shapes can be extruded?
Extruded shapes are mainly divided into three categories:Solid, Hollow, Semi-hollow with partially closed voids.Extrusion has countless applications in many different industries, including construction, automotive, electronics, aerospace, energy and other industries.
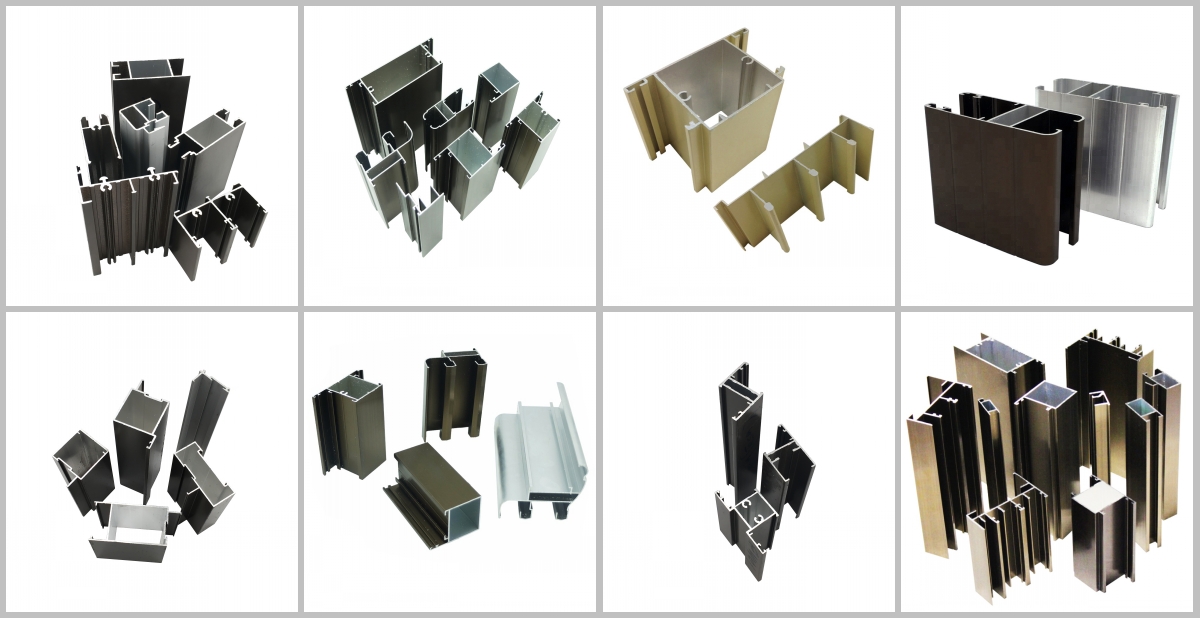
10 steps of aluminum extrusion process
One: Round molds were machined out of H13 steel. Or, if it is already available, pull it out of the warehouse. Before extrusion, the mold must be preheated to 450-500 degrees Celsius to help extend its life and ensure uniform metal flow. After the die is preheated, it can be loaded into the extruder.
Two: A solid cylindrical block of aluminum alloy called a cylinder is cut from a longer log alloy material. Preheat it to between 400-500 degrees Celsius in an oven like this. This makes it sufficiently ductile for the extrusion process, but not meltable.
Three: After preheating the billet, it is mechanically transferred to the extruder. Before loading it onto the press, apply lubricant (or release agent) to it. The release agent can also be used to extrude the die to prevent the blank and die from sticking together.
Four: Now, the extensible billet is loaded into an extruder, where a hydraulic plunger applies pressure up to 15,000 tons. When pressure is applied by the indenter, the billet is pushed into the container of the extruder.

Five: As the alloy material is filled into the container, it is now pressed upward on the extrusion die. With constant pressure, the aluminum has nowhere to go, only through one or more openings in the mold.
Six: After extrusion, the puller will be gripped by the puller, as you can see here, the puller guides it along the beating table at a speed that matches the press outlet. As it moves along the beating table, the profile is "quenched" or evenly cooled by the fan above the sink or table.
Seven: After the extruder reaches its entire table length, it is cut with a hot saw to separate it from the extrusion process.
In each step of the process, temperature plays an important role. Although the extruder has been quenched after leaving the press, it has not yet completely cooled.
Eight: After shearing, mechanically transfer the long profile from the beating table to the cooling table, as you can see here. The contour will remain there until it reaches room temperature. Once this is done, they will need to stretch.

Nine: There is some natural distortion in the outline, which needs to be corrected. To solve this problem, move them to the stretcher. Mechanically clamp and pull the two ends of each profile until it is completely straight and meets the specifications.
Ten: As the table length extrusions now become straight and fully work hardened, they are transferred to the saw table. Here, they are sawn to a predetermined length, usually between 8 and 21 feet. At this point, the characteristics of the extrusion match the tempering of T4. After sawing, they can be moved to an aging furnace to bring them to T5 or T6 status.
Aluminum extrusion is the process of manufacturing parts with a specific cross-sectional profile by pushing a heated alloy material through a die. They can be simple or complex. Can produce 8-24 feet long profiles, which can then be heat treated, finished and manufactured to meet customer requirements